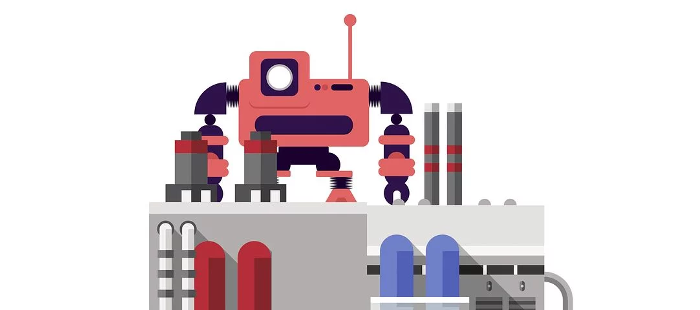
Automation is essentially the use of automated technology and machinery for processes such as manufacturing, eliminating the need of extra labour.
The advantages of automation are:
- Reduced human labour required
- Consistency in quality
- Fewer risks of human error
- Improved health & safety
- Improved efficiency
However, using automation can:
- Be a costly initial investment
- Require some manual labour: observation and programming, for example
- Failures could lead to temporary downtime in production
Automation systems are classed into three different types of automation:
- Fixed automation
- Programmable automation
- Flexible automation
Fixed Automation
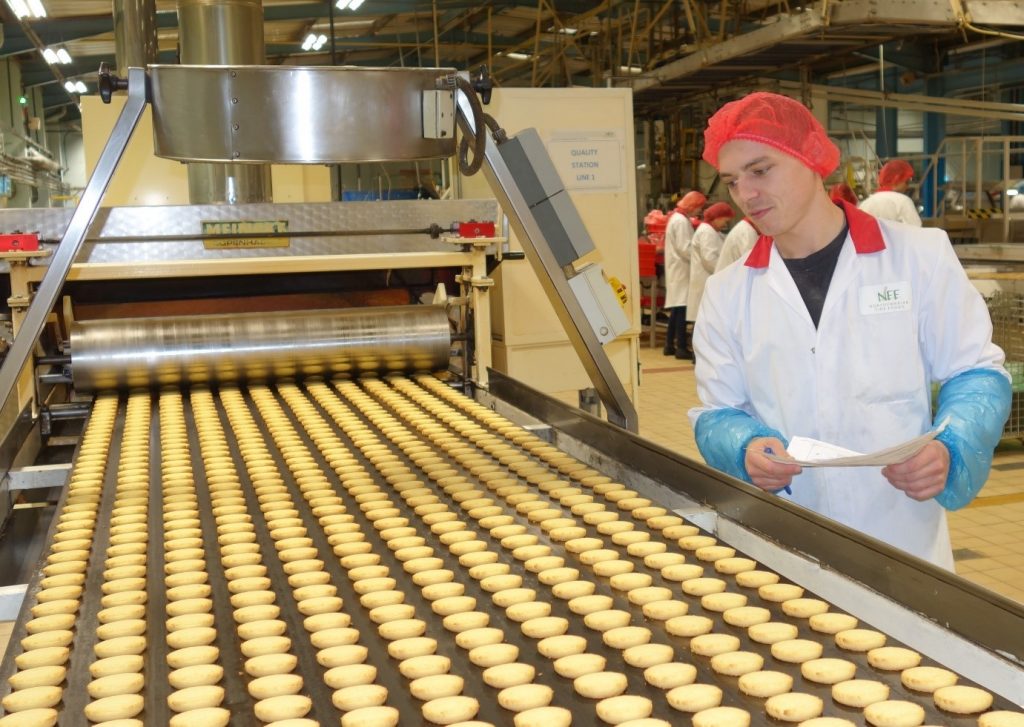
Fixed automation is a type of automation where the process of manufacturing stays fixed by the way it is configured, following a fixed sequence of automated processes. An example of this is flow production, where products are continuously being made. This is often also known as “hard automation”.
Fixed automation can be expensive to set up initially due to the equipment required, but in return, it provides high production rates. However, it is relatively inflexible when it comes to making changes to the product.
This is relatively useful for many companies who use automation to create food products of one type and variant. It allows them to effectively produce that item and package it in bulk.
Foods that require chemical processes, for example, may use this to ensure the consistency of the chemical processes.
Advantages of fixed automation include:
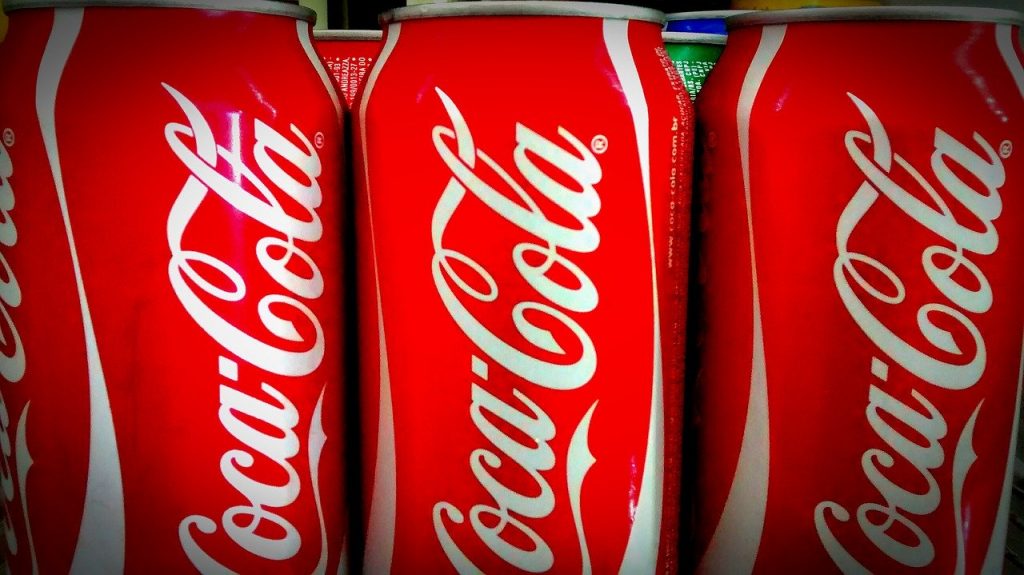
- High levels of production
- Consistent quality in production
- Low cost per unit produced
Disadvantages of fixed automation include:
- High initial cost
- Difficult to accommodate changes
This type of automation is best suited for: High demand and generic products that require no change.
Coca Cola continues to use this automation in their factories. As seen above, this allows for the production of large quantities of the soft drink, allowing Coca Cola to meet the high demands of their classic soft drink.
Programmable Automation
Programmable automation allows the production equipment and automation to be altered to changing needs. This is done by controlling the automation through a program, which can be coded in certain ways for the automation to change the sequence of automation.
It’s used more commonly in low to medium levels of production, often being most suitable for batch production.
Programmable automation will often be used by factories who make different variants of foods. This allows them to make batches, from a few dozen to potentially thousands at a time, of one product. If the product needs changing, it simply needs to be reprogrammed.
Advantages include:
- Flexibility to change products if needed
- Suitable if batch production is required
Disadvantages include:
- Expensive for equipment
- Lower production levels
- Often time-consuming to change products
This type of automation is well suited for: Low/Medium demand and occasional changes in products.
Flexible Automation
Flexible automation, also known as “soft automation”, is similar to programmable automation, although a little more complicated. Essentially, flexible automation enables the production of different types of products without losing time when reprogramming.
A flexible automation system can produce various combinations of products efficiently without having to separate them into different batches, as required in batch production. This type of automation tends to have medium levels of production.
Advantages include:
- Flexibility of products
- No time lost with new changes to production
Disadvantages include:
- High custom machinery/automation cost
- Higher cost per unit
There are essential differences in establishing flexible automation from programmable automation. A flexible automation system will be able to change the physical setup as well as programs, with no loss in time and productivity.
Altering the part programme is usually done by coding the program offline on a computer and then transferring it to the automated system.
This type of automation is best suited for: Medium demand and constant changes/large variety in products.
Deciding which type of automation to use for production can be tricky. This chart below shows what options might be best to consider, depending on the variety and demand of the product.
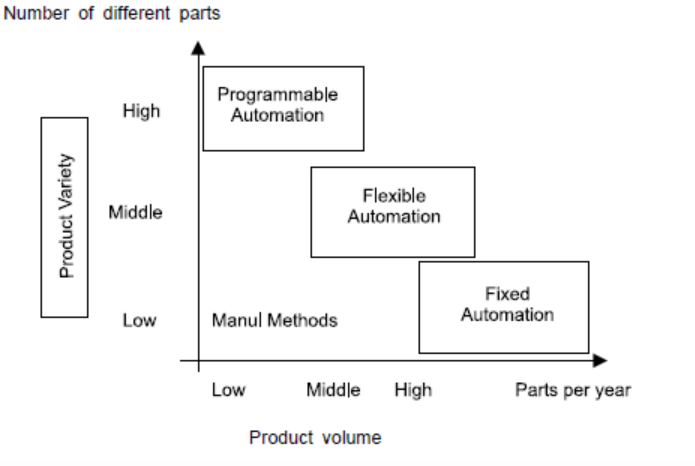
Image courtesy of Wisdomjobs.com
SCADA and MES systems:
SCADA (supervisory control and data acquisition) is a tool which is made of computer systems. It enables for the gathering and analysis of real-time data, and is used to monitor, control and supervise equipment.
These are planted in manufacturing facilities in order to supervise equipment such as telecommunication, water, gas and waste. If there is a problem with these, such as failure in telecommunication equipment, the SCADA system provides information with where the problem has occurred and determines how critical the failure is.
An MES (Manufacturing execution system) is similarly a system which can be used to supervise. However, an MES serves the purpose of monitoring and tracking processes of production in a factory. It allows you to see how effective production is at any given time, which is done by gaining real-time data on production.
Both of these systems can be integrated within your manufacturing process to ensure your factory equipment is working correctly, reducing potential downtime and producing the highest quality product with minimal waste.
If you have any questions about anything covered in this blog or are interested in any of our services, contact us today.