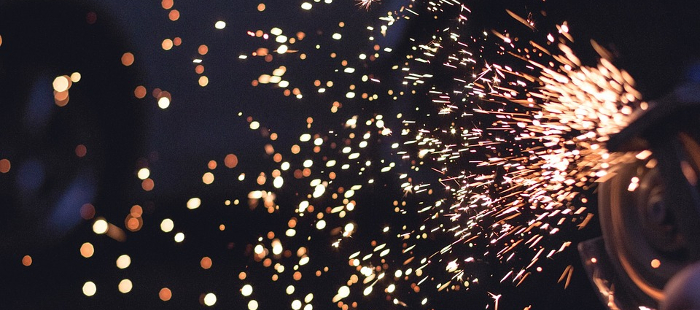
This debate isn’t as simple as human or machine. As automation is adopted in more industries it’s becoming clearer that it fundamentally changes the way a company runs its day-to-day operations. Many companies have adopted automation have discovered the size of the workforce doesn’t change by as much as they may have first thought it would.
This is largely because automation isn’t designed to replace a role within a company, just to complete single repetitive, dangerous and mundane tasks, which often frees up employees to concentrate on more productive tasks and problem-solving.
How automation is transforming the workplace
Many companies in the food industry have adopted automation and control systems. They have discovered that the advancements in technology also bring with them many new skilled positions, which a lot of organisations have filled from their existing pool of talent, although occasionally some retraining has been required.
When automation is adopted correctly it increases productivity and profitability while eliminating the need to manually complete many unskilled tasks. There is a very real danger that those companies that are slow to act will not be able to compete in the market.
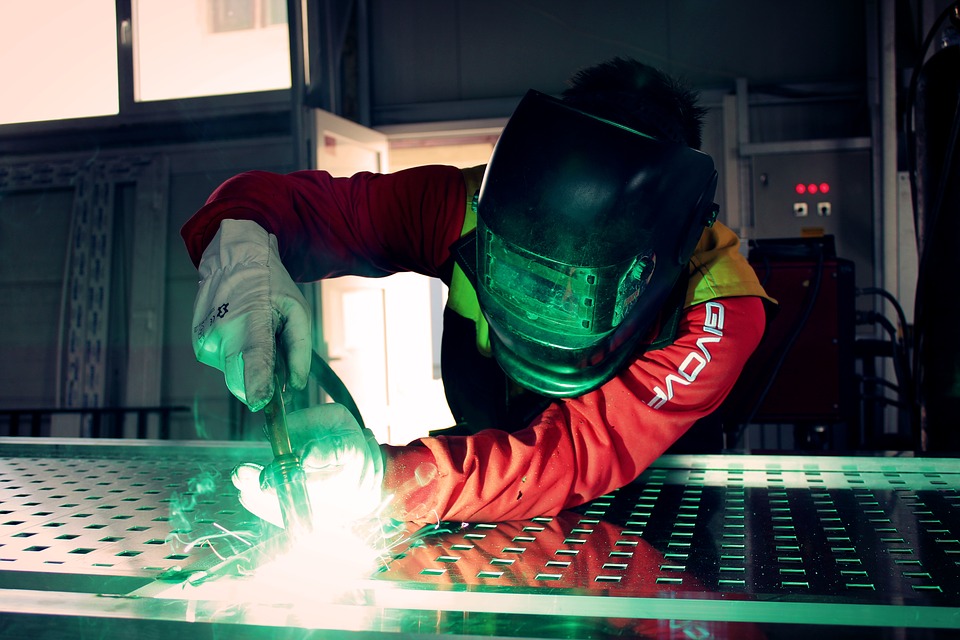
A successful transition
While there are many commonalities across various automation set-ups, a system that unlocks the maximum potential must be well structured, fully integrated, and personalised. Using data-led technology will also provide you with a level of insight that ensures output is always maximised, while your costs are always minimised.
For example, an MES (Manufacturing Execution System) allows for adjustments to be made in real-time based on the production-related data it’s collecting. This constant refinement ensures productivity stays at the required level to meet current demand. These types of systems can also track your inventory and perform quality control tasks. The MES will pull out any items that don’t fall within a defined acceptable criterion, allowing manual inspection of only potentially below par products. Because the process is tracked at every stage, the MES can monitor the performance of each piece of machinery, so if there is a consistently leak wink in the chain it can be flagged for inspection.
Another common system being used in the food manufacturing industry is called SCADA (Supervisory Control And Data Acquisition). SCADA is usually used as more of a pro-active oversight system. It monitors and reports data back to the company, whether on sight or remote, where an employee can use an HMI (Human/Machine Interface) to interact with motors, sensors, pumps, and valves as required. This allows them to refine processes as needed.
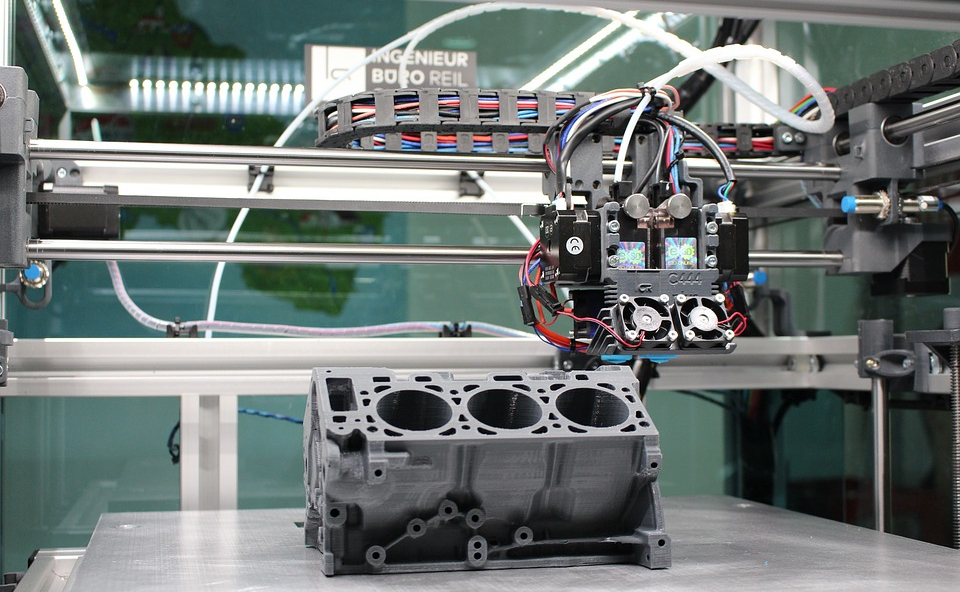
Conclusion
Automation Vs Manual Labour is too competitive. The question should be how you get the most out of automation while leveraging your existing workforce to make the most of it. Successfully integrating automated systems, such as SCADA and MES, requires a bespoke approach. The install must be personalised to the specific needs of each company. When done correctly, companies that embrace automation won’t just be more profitable and efficient, they will be the only companies able to operate competitively in the marketplace.