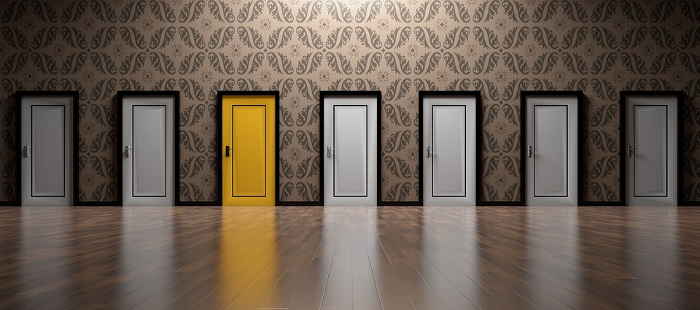
Over the past 20 years, the use of automation in the food industry has increased and equipment has become old, worn out and in many cases obsolete. On top of financial and reliability risks, companies relying on obsolete equipment or software can face heavy fines if they don’t comply with government or industry regulations.
With the rise of so much new technology, software and regulations, it may seem that keeping on top of it all is a near-impossible task. However, now more than ever, managing obsolescence is critical in this constantly changing environment.
Automation technology is changing at a notably faster rate than that of the equipment that it controls. Complications can then arise when systems, equipment and software become a mixture of old and new assets, as when one piece of equipment is replaced it can have knock-on effects to other parts of the process. These complications can sometimes arise in varied and unseen ways.
What are the risks of using obsolete software or equipment?
Technology is evolving at such a rapid pace and by using outdated or obsolete equipment you increase the chances of putting your business at risk. One of these risks is the impact on your productivity.
Evolving technology is designed to increase productivity benefits, so if your equipment is obsolete, it could be slowing your productivity down more than you realise, which can lead to downtime and financial implications. This could be particularly damaging when competing with other businesses. Outdated technology can also limit your ability to respond to the needs of your organisation and the changes in the market.
A business’s performance can also be impacted by technical downsides of using obsolete software, such as data loss, cyber-attacks, data security and limited technical support from software or hardware providers. These risks will not only have critical implications on your production, but employees who interact with your technology may become disengaged and frustrated, leading to poorer performance in the workplace.
How do businesses know if they are at risk of obsolescence?
If a supplier unexpectedly decides to embark on a programme of upgrades, a wide range of products can be rendered obsolete in one sweep. Luckily, manufacturers generally give warnings when equipment or software is reaching obsolescence. These warnings can come at different stages of a product’s life cycle, such as when it has come to the end of life, the last opportunity to buy the product and when the product will no longer be supported. It’s important to note that these warnings may not always be entirely accurate or reliable.
There are a number of proactive approaches businesses can take themselves to keep on top of obsolescence, as it’s essential to review equipment or software sooner rather than later, particularly if it is more than 5 years old. These approaches include keeping tabs on how long equipment has been in place, remaining knowledgeable and vigilant of manufacture dates and how long warranties last, and having a routine upgrading schedule in place when it comes to their technology ecosystem.