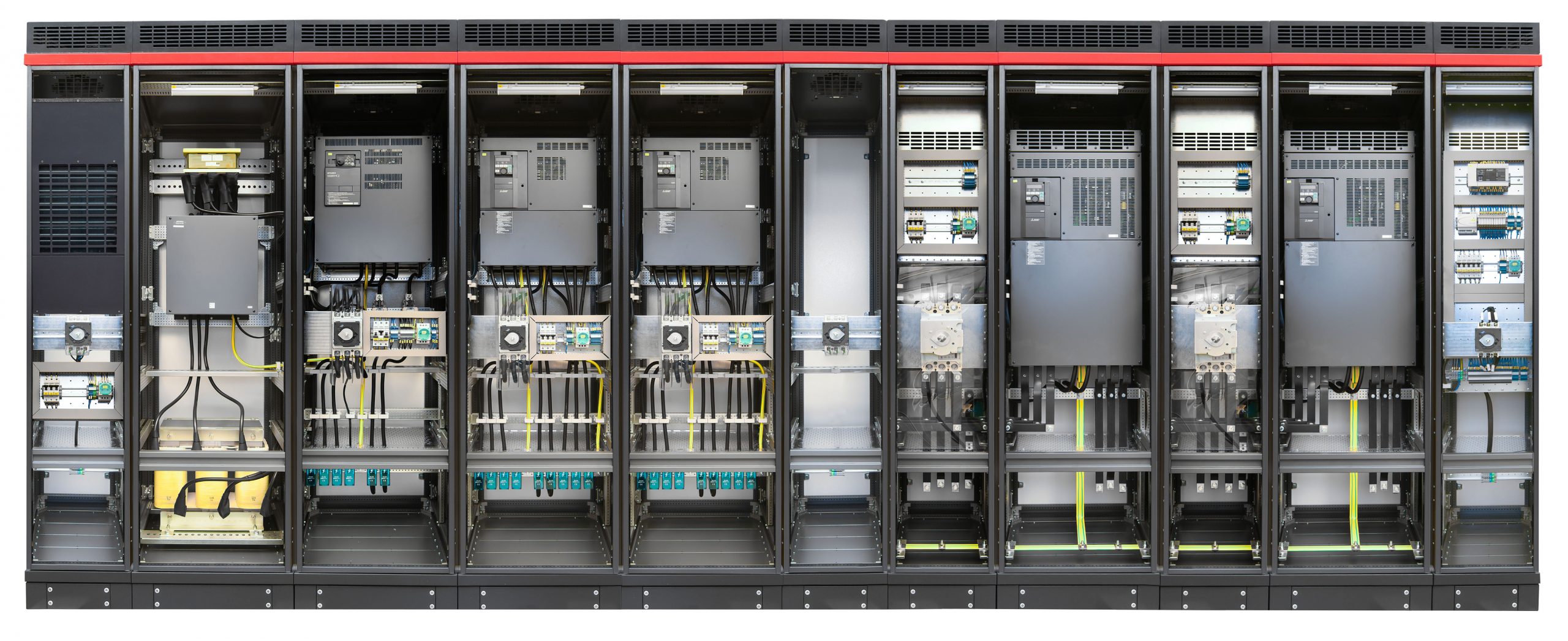
A Programmable Logic Controller, or PLC for short, is essentially a computer. This computer has no display, no keyboard, mouse or any type of hardware you would see on your average desktop computer. It is a complex unit that plays an important role on factory floors, such as in the automation industry or other manufacturing processes and is essential for maintaining a factory floor.
A programmable logic controller has two main parts, a CPU (central processing unit) and an I/O (input/output device), which need to communicate with each other. The I/O can often be integrated into the CPU itself.
Although in most cases, the I/O and CPU are placed together and connected electronically, the I/O does not have to be part of the CPU and can be miles away, as long as both of the devices are communicating with each other, usually through data cables.
When an input is transferred to a PLC, it takes the raw electrical signal and turns it into a programmed readable code, which is then transferred as output and sets an action. For this to happen, the PLC’s CPU has to be programmed through a computer. For example, here the input is the button. The button is pressed, releasing energy through cables to the CPU of the PLC, which turns it into readable information. This is then passed on to the output, an engine, which is then turned on.
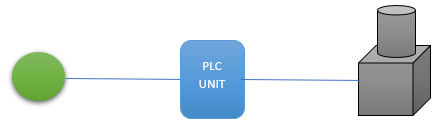
A PLC can also be used to conduct counting and calculations, allowing for the PLC to be used in an observational manner. This allows for easy tracking of data and more, which can be used to show the efficiency and status of production lines.
Some PLC’s, especially larger PLC’s such as rack-mounted ones, allow for communication with other networks, which can be beneficial in a large manufacturing environment, such as in food manufacturing. This is because, through the communication, different production lines for production stages can come together and smoothly transition product from one part of manufacturing to the next.
Choosing a PLC
PLC’s can come in different variants, and different types of PLC’s are best suited for different purposes. When considering what PLC to purchase for an application, there are certain things to look at.
Inputs: It is essential to look at the number of inputs you may require as getting a PLC with little inputs may prove to be inefficient in the long term if more inputs are required.
Outputs: With outputs, it is once again important to list all the output devices that are going to be required.
Safety: Safety is an essential priority, and although PLC’s are all of safe when used properly, certain PLC’s are made for more extreme environments whereas some are not. Locations of the PLC and the environment it is in can have a huge impact.
Programming the PLC
As the name suggests, a programmable logic controller must first be programmed to be fit for use. Most PLCs can be programmed with an application on a laptop/desktop, which can then be transferred to the CPU with the use of ethernet cables, USB cables or other communication devices.
However, programming the controls is not as straightforward. There are many ways to do it, and there is no specific programming language that is used. Most manufacturers use a ladder logic, which can differ in their specifics.
Different manufacturers will, therefore, differ in the language they use.
When changes are made to the program, a PLC can respond to these changes within fractions of a second, making it extremely effective.
What was used before?
Before programmable logic controllers were first introduced, most manufacturing facilities made use of a relay system. This was a lot less effective and involved a system that was turned on and off. This was challenging to use and time-consuming, as well as difficult to change.
Relays tended to be unreliable, often failing and generating a lot of heat due to a large amount of needed electricity.
Examples of PLCs
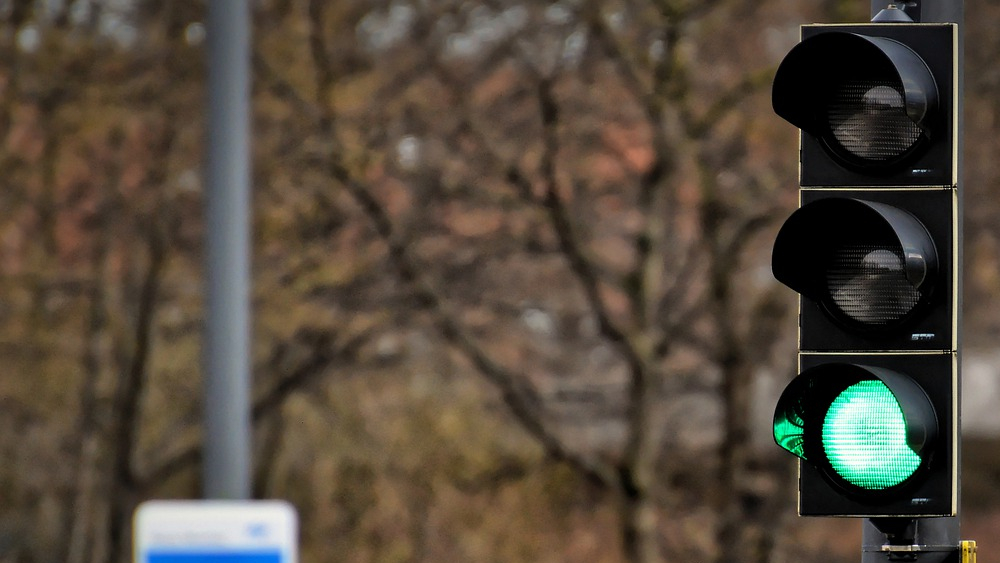
PLC’s are designed in a way to make them reliable for use in harsh industrial environments. With robust construction, a PLC can withstand extreme temperatures, noises, and other industrial environmental features. This makes them perfect for industries such as car manufacturing and other assembly lines.
However, PLCs are used in other places too. Traffic signals, elevators and even washing machines all use a PLC to keep them running. The PLC in a traffic light, for example, performs a set of sequenced tasks, changing the signal light colour accordingly with the pedestrian signal. A power supply is hooked up to a PLC in places like these to keep them working.
Another industry utilising a PLC include glass manufacturing. A PLC can ensure the ratio of raw materials required for the glass manufacturing process is correct, ensuring for maximum efficiency. With an increase of PLC quality, the demand for a PLC in the glass industry is ever-growing.
If you have an industrial environment or are using anything automated which needs to function a certain way with reliability, a PLC is often a useful investment. It is much better than the older relay systems and will allow for automated processes to be reliable and efficient.
If you have any further questions on what we have covered today, or would like to know more about our services, get in touch with us today.