
Smart Condition Monitoring is an innovative set of procedures which scrutinise the working condition of machinery during operation. It is able to identify when something changes while the machine is running, so the operator can make corrections to keep the machinery running before it is severely damaged.
As an approved Mitsubishi delivery partner for predictive maintenance and condition monitoring products and technology, we are able to help your business find the right solution to optimise performance and prevent extended periods of machine downtime, due to malfunction.
How Does the Technology Work?
Mitsubishi Electric has combined a variety of top-of-the-range smart sensing and automation technology into its smart conditioning solution, which is designed to aid with machine imbalance, resonance malfunctions, bearing problems and much more.
This technology increases machine efficiency and ensures that any downtime for repairs is kept to a minimum, by monitoring the status of the following components:
- Fans
- Pumps
- Motors
- Gears
The technology continuously analyses live data using highly advanced measuring sensors, which are then able to send updates and warnings to anything from a smart device to a sophisticated management system. This ensures that the right people are receiving the correct information, so they can take necessary action to prevent total malfunction of a component, thus reducing downtime.
It is also able to detect inconsistencies in the machines’ operating condition by combining smart sensor intelligence with online monitoring and control systems, which run on a series of sophisticated algorithms that can predict failure well ahead of time.
Prevent Down Time on the Production Line
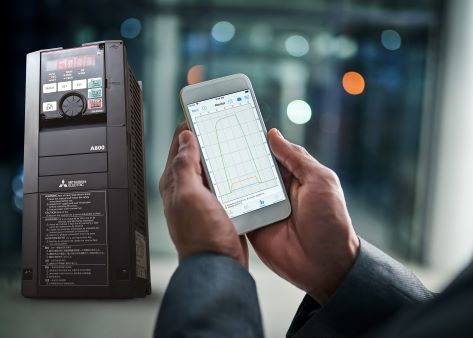
Most production line failures are often not the result of a sudden complication that forces the production line to stop. It is more common that a gradual deterioration of machine parts causes the problem; which means before the malfunction the machine may have been producing inferior goods for longer than you might have realised.
Modern condition monitoring sensor tech can be retrofitted to suit a variety of environments, and taking advantage of these technologies can take a company from preventative to predictive maintenance.
By doing this, a production line can see the warning signs of an imminent failure, which gives repair teams the time to schedule maintenance tasks, rather than having to cope with a failure out of the blue.
Moving from Preventative to Predictive
Predictive maintenance is a huge leap forward, which means that a machine needs only be serviced when required, and not because it’s part of a maintenance routine.
This helps to maximise machine availability, which increases productivity and keeps costs down. Most importantly though, these predictive maintenance solutions aren’t as complicated as they may appear; in fact, they are far more straightforward and cost-effective than you may imagine, and can quite often be built around existing functions that are already implemented within an organisation.
Practical Example: Muntons Malt
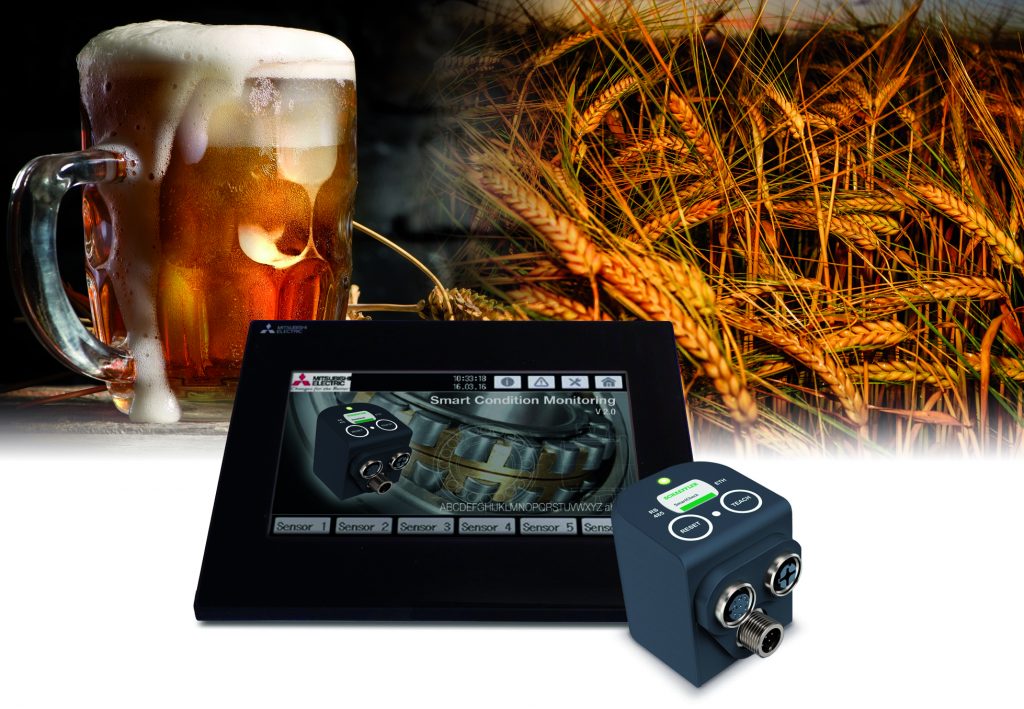
Muntons Malt, one of the largest producers of malted barley in the UK, is currently using a SCM system to protect fans and motors which are crucial to their large-scale operation. The team has previously experienced problems when it comes to difficult-to-reach bearings inside large fan housings; realising after it was too late that the issue had occurred necessitated an unscheduled maintenance stop.
Muntons decided to install an SCM system to two 315kW fans and a smaller 90kW, monitoring the motor, power transmission components and fan shaft bearing on each individual fan. Now the company is aware of the health of the fan systems, as well as having a clear picture of any maintenance work well in advance.
Live information and alarms are displayed on mounted machine interfaces, which the company were able to connect to their previous software automation platform.
If you require any further information about anything we’ve covered in this blog, or you’re interested in any of our other solutions, then why not contact us today?