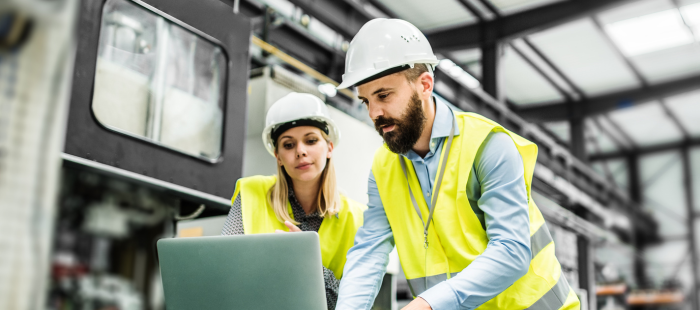
Consistent and thorough maintenance should play an important role in any environment that relies on the operation of manufacturing equipment.
Preventive or predictive maintenance are how most companies operate when it comes to maintaining their production lines, and rightly so, since the third option – reactive maintenance – essentially means allowing a machine to break down before addressing any issues.
In this piece, we’ll be looking at the biggest differences between preventive and predictive maintenance and how you should be integrating each.
What Are the Main Differences Between Preventive & Predictive Maintenance?
Preventative maintenance runs on a scheduled cycle – whether it is really required or not – to pinpoint issues.
Preventive maintenance keeps all components in good working order, however, it fails to take into account the state of the machinery within or the processes required to make it work efficiently.
On the other hand, predictive maintenance occurs when needed, utilising real-time data collection to analyse machine performance for anomalies in operational output to allow scheduled maintenance activity.
In the case that a machine requires maintenance, it can be shut down and repairs can be scheduled at a more convenient time to minimise disruption.
While it’s true to say that any form of downtime can be inconvenient, it’s far better to have the option to schedule this at a time that minimises downtime during busy periods, in comparison to reactive maintenance when costs and downtime can spiral out of control, while the problem is diagnosed and repaired.
In the next section, we’ll take a look at the three types of maintenance in more detail.
What is Reactive Maintenance?
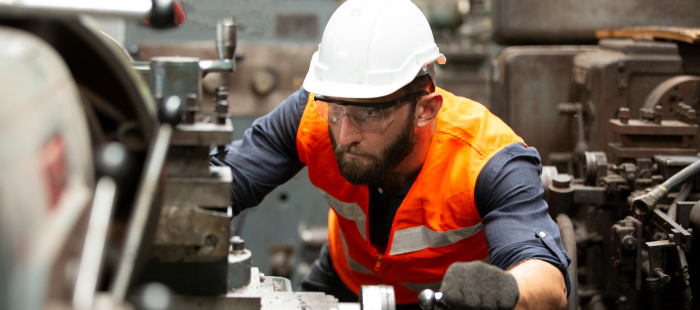
This kind of maintenance is a direct response to any equipment failure or ongoing degradation, and will usually only take place once a machine or component therein has experienced a fault.
It’s for this reason that this kind of maintenance is certainly the least efficient form of maintenance. After all, this only happens once a machine is failing to reach optimal performance – in fact, in most cases this is only once the machine has broken down completely.
This creates further issues with inefficiency and production schedules, since these can happen at any time during the production cycle, rather than being planned for a quieter period.
Of course, to some extent reactive maintenance can never truly be removed, but with both preventative and predictive maintenance strategies in place, it can be severely limited.
What is Preventive Maintenance?
The idea of preventive maintenance is to ensure your production line and its machinery are consistently inspected to prevent issues before they begin to cause a problem. Preventive maintenance must cover the following:
- Planned at regularly scheduled intervals.
- Planned downtime at a time that minimises disruption.
- Must include checks on all equipment and components to carry out calibration, cleaning, repairs and replacements.
- Various levels of inspections – for example, every machine is cleaned and inspected at the end of each day, whereas large scale inspections may only occur on an annual basis, where appropriate.
- Performed whether issues are already identified or not.
Preventative maintenance is a more manual process than predictive maintenance, but it should take place alongside any preventative maintenance system you have to give you the best chance of catching an error before it causes a significant issue.
What is Predictive Maintenance?
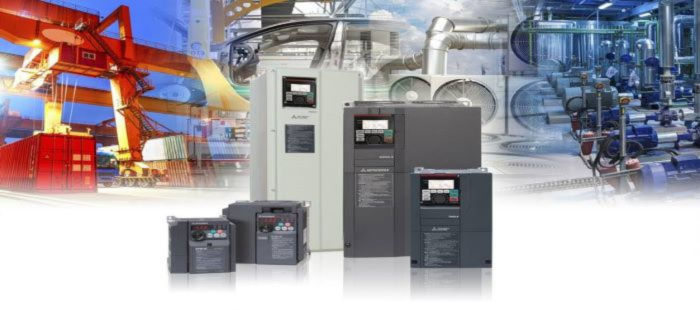
At Control Freaks, we’re specialists in providing predictive maintenance solutions for a range of manufacturing settings. The biggest difference between preventative maintenance and preventative is that this makes use of state of the art predictive maintenance equipment to assess the performance of machinery in real-time with data to identify potential issues on the horizon.
While preventive maintenance is a checklist of historical data and due diligence, predictive maintenance is able to understand machine operations to analyse where an issue is occurring, thereby alerting staff when something requires intervention.
- Proactive maintenance approach.
- Performs in the background as the machine continues to produce as normal, reducing costly downtime.
- Identifies problems early on, allowing staff to schedule vital repairs at a convenient time to prevent complete failure.
- Utilises connected measurement features and data analysis to allow staff to analyse the data in real time.
Preventive vs Predictive Maintenance: Which is Better?

In fact, one of the best means to ensure unexpected downtime is to strike a balance between the two, where both tech and human input can work in harmony for the best results.
This can be beneficial in a number of ways:
Crucial Machinery – For absolutely critical machinery that is the lifeblood of your business, you should implement a predictive maintenance process. This means that the cutting edge technologies can collect data and spot the early signs of a failure, which may otherwise end up costing your business thousands.
By proactively addressing any issues before they have a chance to escalate, you can minimise your downtime, reduce considerable repair costs, and maximise production potential.
Secondary Machinery – Although all machinery is crucial in a production environment, some machinery can be considered as ‘less’ crucial. For any equipment with a lower chance of failure or machinery that can be categorised as of secondary importance, a preventive maintenance schedule can be rolled out.
This involves more manual, yet regularly performed maintenance tasks and inspections, which can keep machinery performing at its most optimal level.
By merging these two strategies, you can truly optimise your maintenance schedule, reallocate appropriate labour more efficiently, reduce unplanned downtime and prioritise tasks based on importance and risk mitigation.
Takeaways
Both preventive and predictive maintenance involve different processes, and while they ultimately work together to achieve the same result, each has their own unique advantages and drawbacks.
Preventive maintenance, with its scheduled checks, can be the best option for businesses with less complex equipment, however it can be time consuming given the manual nature of most of these checks.
Predictive maintenance, on the other hand, does require a bigger initial investment to ensure all your equipment is integrated with the latest technologies, however, we find that these systems pay for themselves given the reduction in repair and downtime costs.
Whatever your choice, you should always ensure that your approach is backed by data and a clear understanding of what your organisation requires to reach your goals within your means.
If you’re looking for expert help to determine which maintenance approach makes sense for your manufacturing setting, or you’re interested in hearing about any of our other products and services, contact us today to find out how we can help.