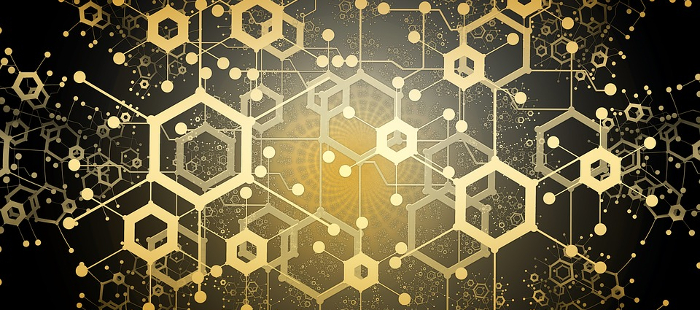
Big data analytics is the new disruptive force in Industry. It’s making waves in food production as manufacturing juggernauts are reimagining process to improve safety standards, facilitate product customisations, and optimise both packaging and distribution.
While there remain many hurdles in adopting big data and technology-led strategies, for those that can afford to do so – the return appears significant.
Reduce Downtime to Optimise Efficiency
Production line downtime and machine outages are a significant drain on any facility. But with the availability of big data, operators are now able to mitigate against the most severe events.
Interconnected systems monitor production lines in real-time, feeding the data back, so supervisors can analyse output alongside monitoring system performance: If a machine shows signs of potential breakdown, the data will flag the risk, and an engineer can step in before a costly unexpected outage.
Moreover, supervisors can pinpoint the optimal time to carry out routine maintenance, minimising disruption and reducing the operational overhead of taking the systems offline.
Improve Quality Control
The food production process has many variables, which can each impact end-product quality. Access to new data points allows manufacturers to monitor these variables on-the-fly – reviewing temperature levels, for example – then make the necessary adjustments to avoid a substandard product.
Such operational efficiencies also improve output as manufacturers automate much of production, mitigating the risk of human error and reducing product wastage. Automated systems can also highlight equipment bottlenecks, enhancing process reliability and further reducing spoilage.
Data analysis can also help optimise the distribution channels, identifying the most efficient means and routes for transporting goods across the world.
Increase Personalisation and Scope for Testing
One challenge in food production is consistency, but so is catering to rapidly-evolving consumer tastes. Product development cycles can be extended, which means manufacturers quickly fall behind the curve with innovation.
Connected systems allow manufacturers to modify formulations using the same production lines, running product tests at scale. While access to data warehouses helps them better predict consumer preferences, then bring new products to market in a more efficient manner.
Furthermore, historical data can provide guidance on elements such as product pricing – a key component in determining viability.
Improve Cost Management Leading to More Sustainable Solutions
There is a global fear as to what automation might mean for employment. However, as tasks become automated, businesses will be able to produce goods at lower costs, improve margins and leave scope for investment in other scalable, job-creating activities.
This could allow manufacturers to review their value chains, leveraging digital capabilities to come up with more sustainable, environmentally responsible approaches.
One such option could be improved sourcing: the world is under strain to produce enough yield to feed a growing population, so data can help manufacturers review agricultural models to adapt their sourcing strategy and optimise crop usage.
Another significant burden on the food industry is wastage, which has a detrimental effect on the environment as much as taking much-needed sustenance away from marginalised areas of society. As manufacturers and packagers analyse and improve waste management, this could cut losses, and perhaps produce new food sources those in need.
If you want to find out more about automation, get in touch. Call us on 01406 424282.